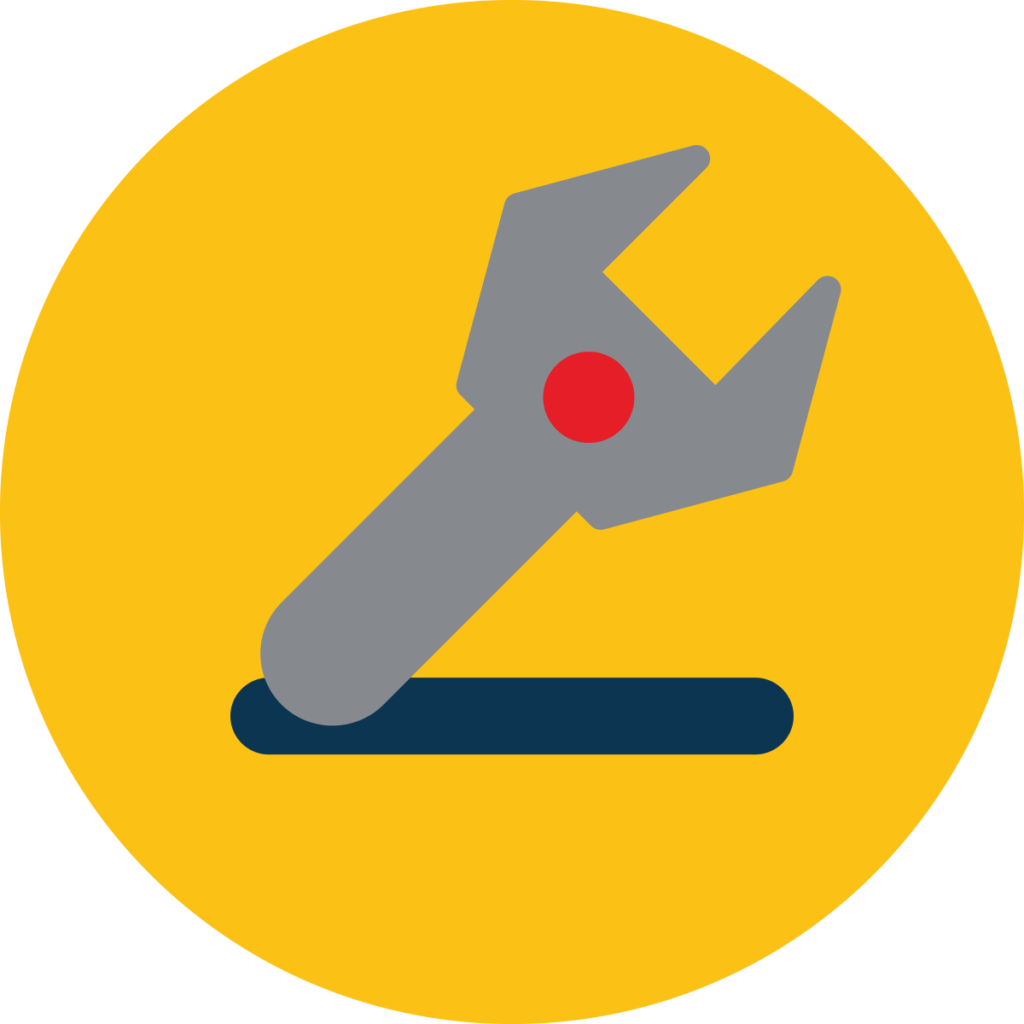
Provides insight into the entire defect process, from detection to resolution
DRS | Defect Reporting System
With the Defect Reporting System we make managing your material more transparant, because you can report defects and keep an overview of the repair process and the life span of your material.
De optimal use of equipment and assets is crucial for adequate slippery control of the road network. Defects occur unexpectedly and are ideally resolved as quickly as possible during the winter season. With the Defect Reporting System you have controle over this by arranging the process according to your preferences. In addition to standard statuses such as ‘Open’, ‘Pending’ and ‘Completed’, you may want to mark a defect with the status ‘On hold’, ‘Not deployable’ and/or ‘Repaired’.
Your management extends as far as the possible defects!
You decide which defects you want to manage from the DRS. Is the focus only on the necessary equipment for spreading actions – the spreaders, plows, brushes and shovels – or would you rather also manage defects in the salt warehouses, the sodium installations, at the support points and power outages? Your management extends as far as the possible defects!
This way you optimize the DRS for your organization, you can switch faster and it also facilitates cooperation with maintenance parties. Agreements made, for example about resolution times, are easy to check, as are additional costs. This makes it quickly clear to everyone where they stand. The statistics are grouped by defect type, machine type or year of construction. The DRS thus provides assistance with and insight into the entire lifespan, from commissioning to the damage and repair process.
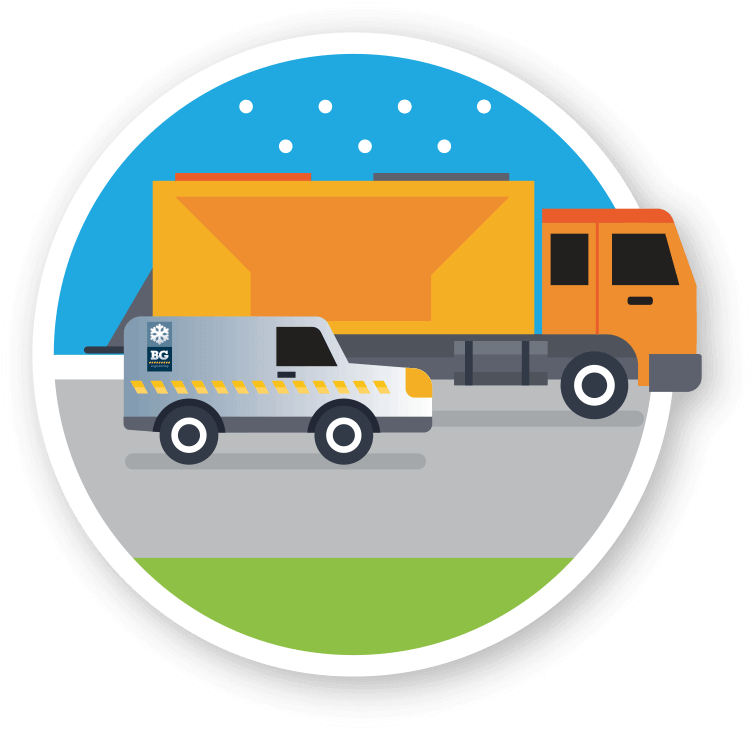
DRS – the advantages
- Systematic reporting of defects is possible
- Good overview of the status of the repairs and usability of your equipment
- From observation to solution: everything is made transparant in one place
- Insight into the types of defects enables improvement of materials and processes
- Easy to manage according to your own wishes, optimized for the organization
- Even more insight and overview by linking the Defect Reporting System to Spreading Action Management
Reports: for continuous improvement
From observation to solution: the DRS provides insight into the process in one place. Here, defects are systematically reported and processed and you can see when the equipment is ready for use again. The smart system makes calculations about the process flow and defect types. Based on this, reports are generated that enable you to anticipate. What types of defects were there per season? What is the distribution of defects per type of machine or year of manufacture? Through this insight, you are able to continuously improve processes, materials and collaborations.
DRS in combination with Spreading Action Management (SAM)
If you also use Spreading Action Management (SAM), data can be correlated and customer-specific reports can be generated. If you have the additional Invoicing module in SAM, damages can be declared automatically.